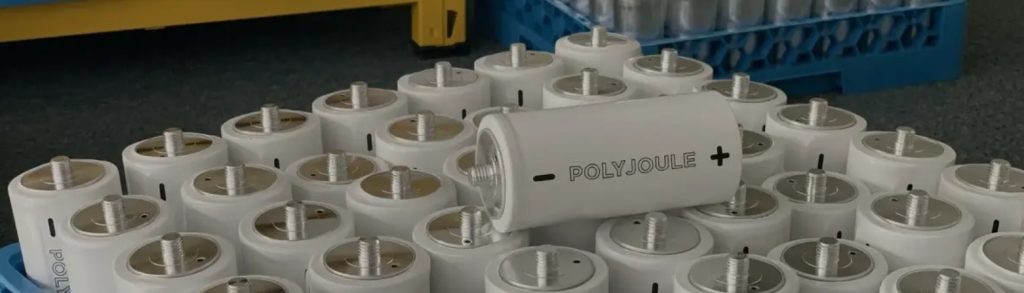
Electricity is a marvelous thing. It can power every manner of machine and digital device, but it is ephemeral. It has to be used as soon as it is created or it is lost forever. The trick to making it serve the needs of humanity is to store it, and to do that, you need a battery.
There are hundreds of ways to make a battery — the Romans did it with copper and iron in a lemon juice bath. But not all of those storage techniques are practical in the real world. Some are too heavy, others too bulky. Many are too costly or use materials that are too scare. Nickel has long been a major component of today’s lithium-ion batteries, but upheavals in some countries masterminded by criminal leaders have caused it to triple in price recently.
Some batteries are good for powering vehicles. Others are better suited to long term grid-scale storage. This report will focus on two new battery technologies that show promise for storing electricity now so it can be used to power homes and businesses later.
Plastic Batteries From PolyJoule
MIT’s Technology Review reports on PolyJoule, a Boston-based company founded by MIT professors Tim Swager and Ian Hunter. They discovered that conductive polymers — specialized plastics — can hold an electrical charge for a long time and charge quickly. They are also efficient, meaning they store a large fraction of the electricity that flows into them. Being plastic, the materials are also relatively cheap to produce and sturdy, holding up to the swelling and contracting that happens in a battery as it charges and discharges.
The conductive polymers replace the lithium and lead typically found in batteries today. By using materials that can be easily created with widely available industrial chemicals, PolyJoule avoids the supply squeeze facing materials like lithium. (It should be mentioned here that virtually all plastics are derived from fossil fuels, although it is possible to make them from sustainable, plant-based materials.)
The PolyJoule batteries could offer a less expensive and longer lasting alternative to lithium-ion batteries for storing electricity from renewable sources like wind and solar. The company is now making its first plastic batteries available. PolyJoule has built over 18,000 cells and installed a small pilot project using inexpensive, widely available materials.
PolyJoule CEO Eli Paster says that the company has focused on building a technology that’s simple to manufacture. It employs a water-based manufacturing chemistry and uses commercially available machines to assemble its battery cells, so it doesn’t need the specialized conditions sometimes required in battery manufacturing.
This is more than a laboratory experiment. The company recently completed a test run of 10,000 battery cells. “For most energy storage startups, having a proof of concept, a single layer pouch cell is a big event. For PolyJoule, being able to produce 10,000+ cells using standard roll to roll processing in non-cleanroom environments, with extremely high manufacturing yields, is a testament to the PolyJoule team and the level of maturity in our chemistry and design. PolyJoule technology works, and it’s ready for large scale deployment,” Paster says.
PolyJoule’s conductive polymer cells span the performance curve between traditional lead-acid batteries and modern lithium-ion cells, while enhancing service life and reducing balance of plant costs, due to their no-HVAC thermal management design. The cells are tested to perform 12,000 cycles at 100% depth-of-discharge. “We see ultra-safe energy storage as a long term capital asset rather than a short term add-on trend in the surging renewables renaissance,” Paster adds. “That means that any chemistry, at the cell-level build, must be fundamentally robust, safe, green, and cost effective over its lifetime. For grid level assets, time scales are measured in decades, not years.”
At present, the PloyJoule batteries cost about $65 per kWh. Many industry observers believe costs must get down to $20 per kWh or less for battery storage to really force a sea change in how electricity is made and stored, but keep in mind that economies of scale are still ahead for the fledgling company. Not only that, the cost of traditional lithium-ion batteries is trending up rather than down, thanks to unstable commodity prices. The other side of the coin is that plastic batteries promise to last longer before needing replacement and cost less to maintain.
A drawback to plastic batteries is that they have significantly lower energy density than conventional lithium-ion batteries, which means they require up to 5 times as much room for an equivalent storage capacity. On the other hand, they don’t need any active temperature control systems to make sure they don’t overheat or catch fire. “We want to make a really robust, low cost battery that just goes everywhere. You can slap it anywhere and you don’t have to worry about it,” Paster says.
Freeze/Thaw Battery For Grid-Scale Long Term Storage
How long is long term? Today’s conventional lithium-ion grid-scale battery storage facilities typically can supply electricity to the grid for about 4 hours. They are also optimized for regular daily use. Charge up during the day when the sun is shining or the wind is blowing, then discharge in the late afternoon and early evening when the demand for electricity spikes. They aren’t really designed to store electricity for days, weeks, or months.
PolyJoule’s plastic batteries might be able to store energy longer, but many people are starting to think about seasonal storage — charge up in the spring and summer when the sun shines brightest and blustery winds set turbines spinning, then draw on that stored energy in the winter when renewables are less able to meet the demand.
Engineers at Pacific Northwest National Laboratory say they have developed a freeze/thaw battery that is well suited for supporting the electric grid by storing energy for months, giving utilities the ability to supply electricity during power outages due to severe storms, natural disasters, accidents, or vandalism. The key to freeze/thaw batteries is the electrolyte, a form of salt that is liquid at higher temperatures, but solid at room temperature.
The battery is charged by heating it up to 356°F, which lets ions flow through the liquid electrolyte to create chemical energy. The battery is then cooled to room temperature, essentially locking in the battery’s energy when the molten salt solidifies and the ions that transfer energy remain nearly still. When energy is needed, the battery is reheated and the electricity flows. According to Machine Design, the researchers have built a prototype of the freeze/thaw battery which is about the size of a hockey puck. In tests, it retains 92% of its capacity over a 12-week span.
The team also avoided rare and highly reactive materials to ensure larger batteries would be relatively inexpensive. The anode and cathode, for example, are simply solid plates of aluminum and nickel. The team added sulfur — another common, low cost element — to the electrolyte to enhance the battery’s energy capacity. The separator between the anode and the cathode is nothing more than fiberglass, which can be used because of the battery’s stable chemistry. Fiberglass cuts costs and makes the battery sturdy enough to survive the freeze/thaw cycles. Most higher temperature molten salt batteries need expensive ceramic separators, which are susceptible to breaking due to temperature changes.
The battery stores energy at a materials cost of about $23 per kWh, but that was calculated prior to the recent jump in the cost of nickel. The team is exploring the use of iron, which is less expensive, in hopes of bringing the materials cost down to around $6/kWh. The battery’s theoretical energy density is 260 Wh/kg, which is higher than most lead-acid and flow batteries,
The researchers point out that batteries used for seasonal storage would likely charge and discharge just once or twice a year. Unlike batteries designed to power electric cars, laptops, and other consumer devices, they don’t need to withstand hundreds or thousands of cycles.
“We envision something like a large battery on a 40-ft tractor-trailer parked at a wind farm,” says Vince Sprenkle, senior strategic advisor at PNNL. “The battery is charged in the spring and then the truck is driven down the road to a substation where the battery is available if needed during the summer heat.”
The Takeaway
Today, the electrical grid has several layers of energy providers. Some offer steady, reliable, dependable electricity all day, every day. Any that is not used immediately is wasted. These baseload sources are typically coal-fired or nuclear facilities that cannot ramp up quickly to meet sudden increases in demand.
For that, utilities rely on so-called peaker plants, generating stations that get brought online for a few hours each day to meet the demand in the late afternoon and early evening when people get home from work, turn up the AC, switch on the TV, and begin cooking dinner. Today’s grid-scale storage batteries are able to match or outperform those peaker plants but not the baseload generators. That’s where these new plastic or freeze thaw batteries may find success.
Battery stories are always speculative. The transition from laboratory to commercialization is fraught with danger and many of these exciting new technologies will never make it in the marketplace. We are not suggesting either of these technologies will go mainstream. Our only intent is to keep our readers informed about the newest developments that have some likelihood of success.
In the end, the grid storage solutions of the future may involve neither of these, but that $6 per kWh number for the freeze/thaw molten salt battery does get us pretty excited. That’s a number at which renewable energy would not become just nice to have, it would make it imperative and render all other electricity generating strategies obsolete.