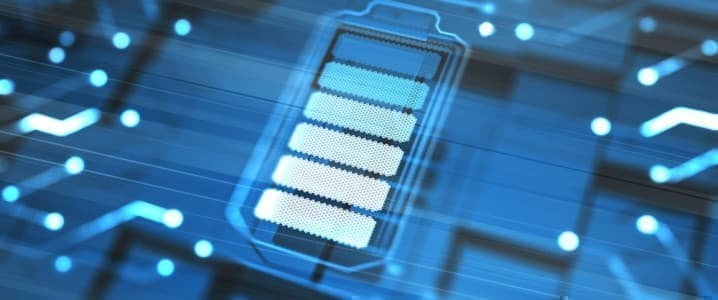
The last twelve months proved turbulent for the electrical products market. This is true whether you’re a raw material miner, refiner, manufacturer, or end user. Indeed, ongoing issues with battery metal prices and supply security affected millions. After demand rose dramatically, Chinese battery makers began snapping up resources left and right. This left major automakers scrambling to shore up supply agreements for raw materials and the associated downstream battery supply chains. Both cost and security of supply have become significant concerns across both commercial and defense industries. In fact, these worries have made it all the way to the White House. As with rare earth metals, the reliance on overseas supply sources leaves the supply chain dangerously exposed.
That’s why this week was the perfect time to catch up with David Klanecky. He is the CEO of North America’s largest and arguably most professional battery recycling company, Cirba Solutions.
Driving the Recycling of Battery Metal and Components
Cirba Solutions currently operates six processing facilities across the USA. In September, they announced a seventh, which the company intends to construct in Arizona. By 2026, they hope to have at least 13 fully operational facilities. Above all, Cirba Solutions recognizes that both the availability and demand for recycled battery materials need to expand rapidly over the next decade. In fact, this is driving a more than $200 million investment in an existing facility in Ohio.
“The need for critical minerals is heightened with a focus on the electrification movement in transportation and will continue to accelerate,” says Klanecky. “Over the next five years, there will be more attention on recycled content and domestic supply.”
What’s more, the company sees a closed-loop domestic recycling industry as critical. This is not only for self-sufficiency, but for environmental reasons. Without an adequate recycling industry, electronic components like batteries will only continue to end up in landfills.
Battery Metals: Full Range of Services
Klanecky explains, “In the circular battery supply chain, we do everything from collection, safe packaging, transportation, and storage to the end point of processing them and seeing those materials to be used again. We’re doing this with a focus on sustainability and safety while also generating profits for our shareholders.”
However, the lithium-ion and nickel-cadmium battery recycling industries are still in their infancy. Cirba Solutions is a market leader in all battery chemistries, including lithium-ion and lead acid battery recycling. They can confirm that the US recycles around 99% of lead acid batteries. Moreover, around 95% of the lead will be recovered and reused. But in the case of consumer electronics, recycling rates are only around 10%.
We all share responsibility for that. After all, how many old phones, speakers, and portable chargers do each of us have lying in drawers? Many of us would be quite embarrassed to answer.
A Proven Recycling Model in Need of Infrastructure
Fortunately, that upside potential gives the growing recycling industry a considerable target market. Unlike rare earths, which struggle for profitability amidst mining, refining, and recycling, battery metal recycling companies like Cirba Solutions have been profitable for years. Even better, they provide battery makers with refined salts (such as the sulfates of nickel, cobalt, and manganese), lithium carbonate, and graphite at prices and purity levels competitive with those for imported products. More often than not, the latter come from China and are the direct result of resource mining.
That said, the technology involved remains both sophisticated and capital-intensive. It involves mechanical separation, chemical extraction, and refining. Therefore, it necessitates specialist facilities depending on the product inputs. For instance, lead acid products require a different process from nickel, cadmium, or lithium-ion batteries.
Also, the nationwide collection and safe transport of these materials are key to growing the industry. After all, some of these items are potentially hazardous, and need to be treated with the utmost care. Therefore, an organizational infrastructure that can accommodate all battery types is critical to successfully rolling out an end-to-end closed-loop system.
“We’re doing that work right now,” says Klanecky. “We pride ourselves on collection, packaging, and logistics. Our expansive footprint for our services is a differentiator that has taken years to develop, and it’s something our customers appreciate having access to.”
We Need a Vision For Better Battery Metal Recycling
In reality, it’s often much easier to create collection agreements for EV batteries. This is mainly due to their mass and focused end-of-life options like auto dealers and specialist breaker’s yards. In fact, Toyota has had such a system in place for its Prius batteries for over a decade.
However, when it comes to consumer electronics, it would take much more complex collection arrangements covering multiple channels. Without that, it would be hard to make any serious in-roads towards exploiting the opportunity to recycle all products. Fortunately, there is a working precedent in Cirba Solutions’ existing structure, even if recycling rates have only reached 10% thus far. Still, it would take a paradigm shift in consumer attitudes to achieve the levels of recycling seen in lead acid or EV batteries.
One thing we can prove is that some consumers are willing to actively recycle items, even when there’s a relatively low financial return for them. And with economies of scale come new opportunities to offer modest financial incentives in return for increased recycling rates.
On the other hand, there remains a significant potential to exploit its other natural resource – recycled batteries and devices. If we make the right investments now, the US recycling industry could become a crucial part of the supply chain in the years ahead.