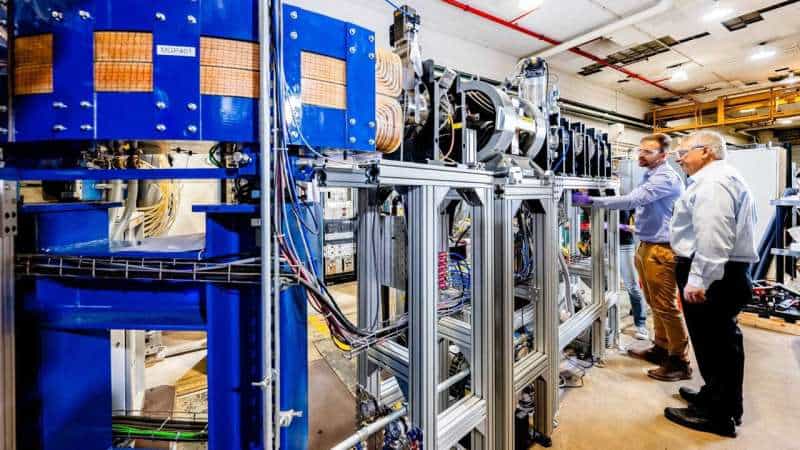
Nickel-based alloys, critical materials used in many advanced nuclear reactors, come with unwanted baggage. Aside from being very expensive, nickel ore is mined in politically sensitive parts of the world. The ore also has a high moisture content that can pose safety issues for those transporting the ore in cargo ships because the cargo can slosh around and create a load imbalance.
Despite nickel’s comparable strength and several notable advantages over steel—including heavy resistance to corrosion and a structure that can withstand the harsh environments inside nuclear reactors—scientists would like to discover alternate materials.
Nuclear science and technology experts at the U.S. Department of Energy’s (DOE) Argonne National Laboratory have been working for the past two years to develop a framework to accelerate the discovery of new nuclear reactor-appropriate materials. These new materials would be used in place of critical minerals like nickel alloys.
Discovery of appropriate new materials is important because advancing next-generation nuclear power is central to U.S. efforts to produce clean energy and meet decarbonization goals.
“With this new framework, we have more input from multi-physics simulations to make sure each iteration gives enough improvement. We make sure each change would be beneficial and that helps us speed up the optimization procedure,” said Yinbin Miao, of Argonne National Laboratory.
“It takes a very complex procedure to demonstrate and qualify a coating for use in a nuclear reactor,” explained Yinbin Miao, an Argonne principal materials scientist and lead investigator on the team conducting the research.
“By using a multi-physics model informed by experimental measurement, we have more insights on different aspects of the problem. That’s helping us find the optimized recipe or thickness of different layers that use nickel alloys. It helps us understand what material composition will be needed so we have a model to accelerate optimization speed.”
Miao has experience in multi-physics simulation of nuclear systems and material performance analysis under harsh conditions in nuclear reactors. Sumit Bhattacharya, also a principal materials scientist, is a coating expert for extreme environment applications. He focuses on identifying advanced material coating architecture, and its development and optimization for complex designs.
Principal nuclear engineer Ed Hoffman models the techno-economic benefits of each new material and how each material does or does not affect reliance on critical materials. Ahmed Amin Abdelhameed, a nuclear engineer, is an expert in neutronics and studies changes in a reactor’s performance based on the behavior of materials studied in the experiments.
Additionally, postdoctoral researcher Soon Kyu Lee helps the team with modeling and Wei-Ying Chen, another Argonne principal materials scientist with expertise in materials characterization, helps measure some key coating properties needed for simulations.
“Previously, we’d do a test that reveals a material is not good enough, then we’d change some parameters and eventually get a more optimal solution,” Miao said. “With this new framework, we have more input from multi-physics simulations to make sure each iteration gives enough improvement. We make sure each change would be beneficial and that helps us speed up the optimization procedure.”
A key quality the team looks for in candidate materials is corrosion resistance. This quality is needed because the inside of a nuclear reactor is an intense radiation and high-temperature environment. Material coatings must possess mechanical strength but they also need to demonstrate resistance to corrosion during both normal operations and accident scenarios.
To study corrosion resistance and material strength of one promising material, the team used a new capability at the Argonne Tandem Linac Accelerator System (ATLAS), a DOE Office of Science user facility.
They bombarded their target with ATLAS’s heavy ions to simulate the high radiation conditions inside a reactor. The new ATLAS Materials Irradiation Station degraded the material’s properties as much in a day as a nuclear reactor does in a year, minus the long-lasting radioactivity. They demonstrated that the new material could indeed withstand reactor conditions and resist corrosion.
“We wanted to build a framework that works for different coatings but we also needed to provide a demonstration case,” Miao said. “Otherwise, it was just a framework example without any demonstration.”
The team will file a patent for the new coating material and is currently seeking more funding to further investigate its properties.