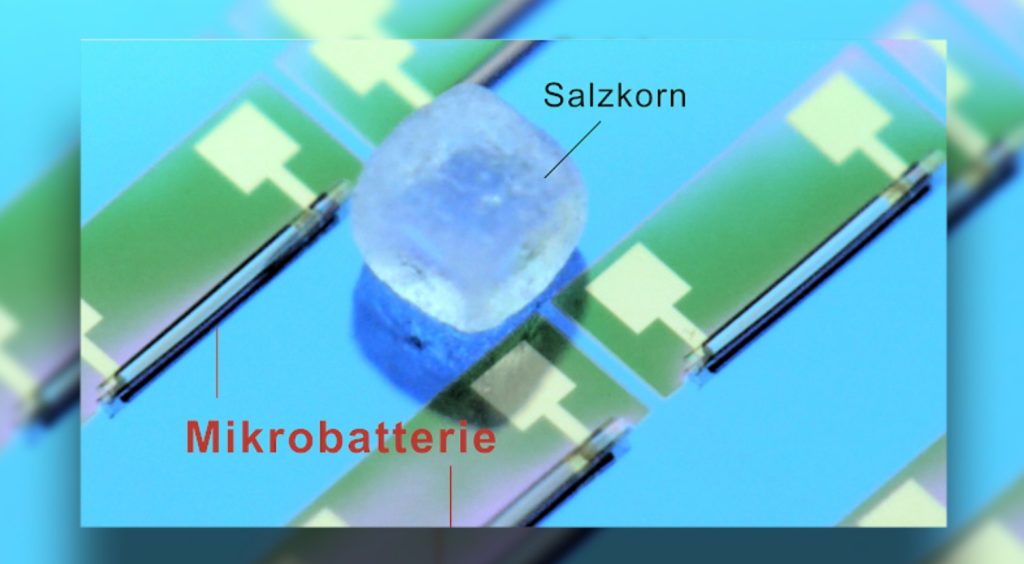
Computers are getting smaller and smaller, just as current cell phones offer computing power similar to that of a laptop. And the trend toward miniaturization continues. Smart dust applications (tiny microelectronic devices), such as biocompatible sensor systems in the body, demand computers and batteries smaller than a dust mote. So far, this development has been hindered by two main factors: lack of on-chip power sources for operation anytime and anywhere and difficulties in producing integrable microbatteries.
In the current issue of the prestigeous and highly cited journal Advanced Energy Materials, Prof. Dr. Oliver G. Schmidt, head of the Professorship for Material Systems of Nanoelectronics and Scientific Director of the Center for Materials, Architectures and Integration of Nanomembranes (MAIN) at Chemnitz University of Technology, Dr. Minshen Zhu, who has been working in Prof. Schmidt’s group at the Research Center MAIN since February 2022, and researchers from Leibniz Institute for Solid State and Materials Research (IFW) Dresden and Changchun Institute of Applied Chemistry present a solution to these challenges. They discuss how battery-powered smart dust applications can be realized in the sub-millimeter-scale and present the world’s smallest battery by far as an application-oriented prototype.
“Our results show encouraging energy storage performance at the sub-square-millimeter scale”, says Dr. Minshen Zhu, and Prof. Oliver Schmidt adds: “There is still a huge optimization potential for this technology, and we can expect much stronger microbatteries in the future.”Beyond the limits of miniaturization
The power to run tiny sub-millimeter-scale computers can be provided by developing appropriate batteries or “harvesting” methods to generate electricity.
In the area of “harvesting,” micro-thermoelectric generators, for example, convert heat to electricity, but their output power is too low to drive dust-sized chips. Mechanical vibrations are another source of energy for powering tiny-scale devices. Small photovoltaic cells that convert light into electrical energy on small chips are also promising.
However, light and vibrations are not available at all times and in all places, making on demand operation impossible in many environments. This is also the case, for example, in the human body, where tiny sensors and actuators require a continuous power supply. Powerful tiny batteries would solve this problem.
However, the production of tiny batteries is very different from their everyday counterparts. For example, compact batteries with high energy density, button cells for instance, are manufactured using wet chemistry. Electrode materials and additives (carbon materials and binders) are processed into a slurry and coated onto a metal foil. On-chip microbatteries produced using such standard technologies can deliver good energy and power density but have a footprint of significantly more than one square millimeter.
Shrinking Tesla technology: Swiss-roll process enables on-chip batteries for dust-sized computers
Stacked thin films, electrode pillars or interdigitated microelectrodes are used for on-chip battery manufacturing. However, these designs often suffer from inferior energy storage, and the footprint of these batteries cannot be reduced significantly below one square millimeter. The goal of Prof. Schmidt, Dr. Zhu and their team members was therefore to design a battery significantly less than one square millimeter across and integrable on a chip, which still has a minimum energy density of 100 microwatt hours per square centimeter.
To achieve this, the team winded up current collectors and electrode strips at the microscale – a similar process also used by Tesla on the large scale to manufacture the batteries for its e-cars.
The researchers use the so-called “Swiss-roll” or “micro origami” process. A layered system with inherent tension is created by consecutively coating thin layers of polymeric, metallic and dielectric materials onto a wafer surface. The mechanical tension is released by peeling off the thin layers which then automatically snap back to roll up into a Swiss-Roll architecture. Thus, no external forces are needed to create such a self-wound cylinder micro-battery. The method is compatible with established chip manufacturing technologies and capable of producing high throughput micro-batteries on a wafer surface.
Using this method, the research team has produced rechargeable microbatteries that could power the world’s smallest computer chips for about ten hours – for example, to measure the local ambient temperature continuously. A tiny battery with great potential for future micro- and nanoelectronic sensorics and actuator technologies in areas such as the Internet of Things, miniaturized medical implants, microrobotic systems and ultra-flexible electronics.