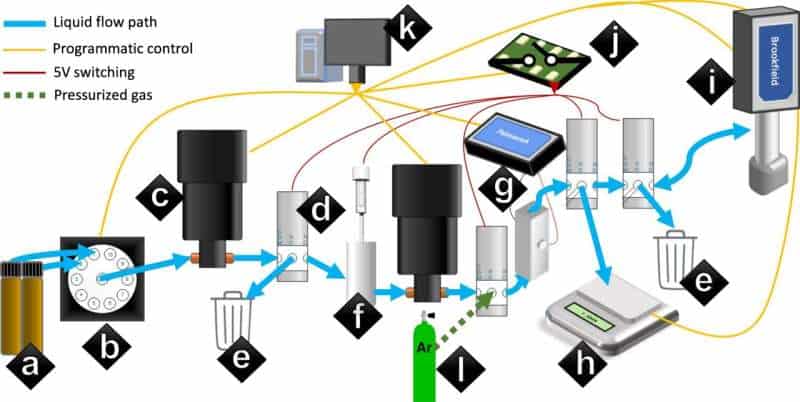
As sales of handheld devices have skyrocketed and car makers have turned to electric vehicles, demand for batteries that last longer and charge more quickly has risen as well. Unfortunately, the science of developing new batteries to serve such needs has lagged—it typically involves the use of intuition on the part of chemists along with persistence. Such efforts can take years. In this new study, the researchers in Pittsburgh sought to speed up the process by using automation techniques.
At the heart of most battery design is the creation of a non-aqueous lithium-ion battery electrolyte that works better than those that have been developed before. Researchers tend to shoot for optimized ion conductivity. To speed up the process of finding them, the researchers created a robot called Clio that accepted the ingredients used to make an electrolyte and then followed a set of instructions to make some samples.
They then added a computer running a deep learning AI application (called Dragonfly) that accepted data from Clio and from sensors in the electrolyte that was produced by the robot. Dragonfly analyzed the sample then suggested possible improvements. Clio accepted the improvements and used them to make a new sample. This back-and-forth system was repeated multiple times (each took approximately two days) with the electrolyte gradually improving. At a point designated by the researchers, the mechanical pair ceased operating, allowing the researchers to test the products that had been produced.
In their testing, the researchers found that their paired-system worked as hoped, they saw gradual improvements in the electrolyte samples—the best was found to be 13% better than top performing batteries now on the market.
Moving forward, the researchers plan to continue refining their system to allow for testing more objectives and perhaps to make it run faster.