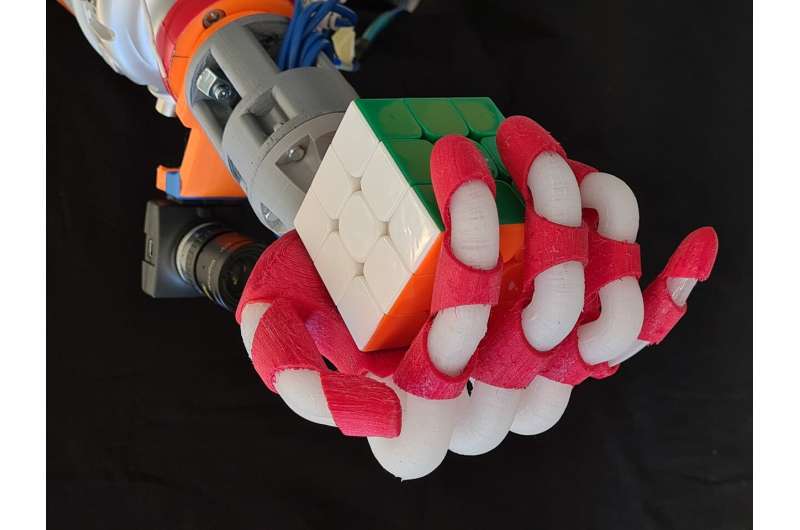
Robots based on soft materials are often better at replicating the appearance, movements and abilities of both humans and animals. While there are now countless soft robots, many of these are difficult to produce on a large-scale, due to the high cost of their components or their complex fabrication process.
Researchers at University of Coimbra in Portugal recently developed a new soft robotic hand that could be more affordable and easier to fabricate. Their design, introduced in Cyborg and Bionic Systems, integrates soft actuators with an exoskeleton, both of which can be produced using scalable techniques.
“Most robots are made of rigid materials,” Pedro Neto, one of the researchers who carried out the study, told Tech Xplore. “However, when we observe animals, we notice that their bodies can be composed of hard parts (skeletons) and soft parts (such as muscles). Some animals, like earthworms, are entirely soft-bodied. Taking inspiration from nature, we anticipate that the next generation of robots will incorporate components made of soft materials or, in some cases, they can be entirely soft-bodied.”
Compared to rigid robots, soft robotic systems could be safer and could better co-exist with humans or animals in both outdoor and indoor environments. For instance, if they collide with humans, animals, or objects in their surroundings, these robots are less likely to cause significant damage or injuries.
The key objective of the recent work by Neto and his colleagues was to develop a new soft robotic hand that is both safe and affordable. Such a hand would theoretically be easier to deploy on a large-scale, thus fueling new research and innovation in the field of robotics.
“We leveraged finite element analysis to optimize the design before physically fabricating the hand, reducing prototyping costs,” Neto explained. “The utilization of regular 3D printing proved effective by directly printing some components in soft materials and printing molds in rigid materials.”
The soft robotic hand created by Neto and his colleagues is based on several different materials. Its carefully designed structure was meant to replicate the appearance and functionality of human hands, reproducing their movements and abilities.
“The robotic hand’s configuration consists of five soft actuators, each corresponding to a finger, and an exoskeleton to promote finger’s bendability,” Neto said. “An ON-OFF controller maintains the specified finger bending angles, enabling the hand to effectively grip objects of varying shapes, weights, and dimensions.”
The researchers so far evaluated the performance of their robotic hand in a series of simulations and experiments. Their initial results are highly promising, as the hand could successfully grasp numerous objects with different shapes, weight, and sizes.
“The primary contribution is the integrated design-fabrication system that utilizes finite element analysis to optimize the design prior to their fabrication,” Neto said. “This achievement has the potential to increase the accessibility of soft robotic hands while lowering costs and eliminating the typically time-consuming design-fabrication procedures, which frequently rely on resource-intensive iterative workflows.”
In the future, the soft robotic hand developed by this team of researchers could be used by both academic teams and individual roboticists to test new artificial intelligence (AI) algorithms and other computational tools aimed at advancing robot abilities. In addition, its design could open new avenues for the low-cost fabrication of humanoid robots that can assist humans with their everyday activities.
“Our next studies will focus on improving the fabrication of soft actuators and sensors, aiming to enhance the accessibility of soft robots to a wider audience,” Neto added. “The control of soft robots using artificial intelligence is another research topic that we are working on.”