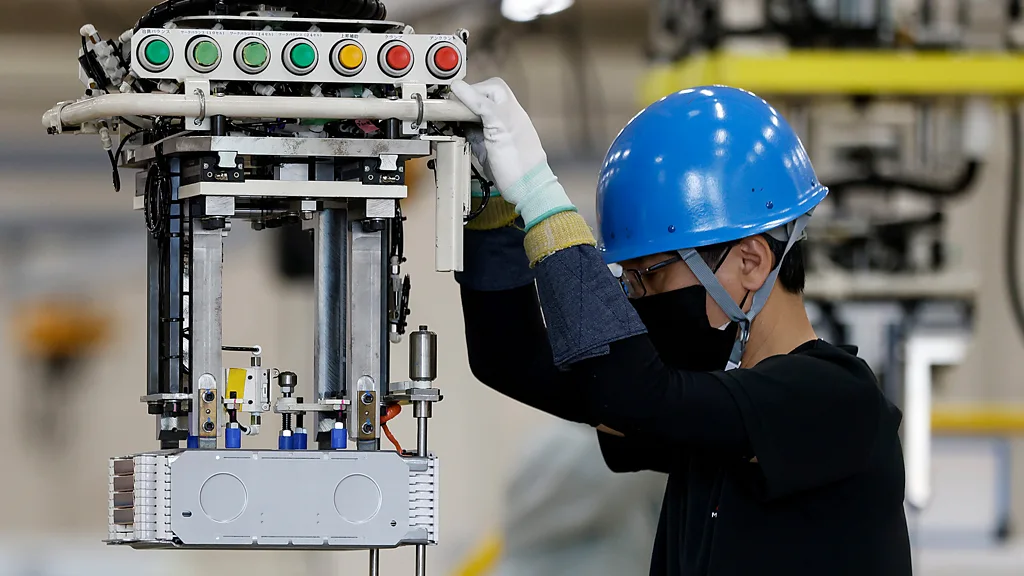
Lithium batteries are very difficult to recycle and require huge amounts of water and energy to produce. Emerging alternatives could be cheaper and greener.
In Australia’s Yarra Valley, new battery technology is helping power the country’s residential buildings and commercial ventures – without using lithium. These batteries rely on sodium – an element found in table salt – and they could be another step in the quest for a truly sustainable battery.
The global demand for batteries is surging as the world looks to rapidly electrify vehicles and store renewable energy. Lithium ion batteries, which are typically used in EVs, are difficult to recycle and require huge amounts of energy and water to extract. Companies are frantically looking for more sustainable alternatives that can help power the world’s transition to green energy.
“Sodium is a much more sustainable source for batteries [than lithium],” says James Quinn, chief executive of Faradion, the UK-based battery technology company that manufactures the sodium-ion batteries for Yarra Valley utility company Nation Energie. “It’s widely available around the world, meaning it’s cheaper to source, and less water intensive to extract,” says Quinn. “It takes 682 times more water to extract one tonne of lithium versus one tonne of sodium. That is a significant amount.”
Faradion’s sodium-ion batteries are already being used by energy companies around the world to store renewable electricity. And they are just one alternative to our heavy and growing reliance on lithium, which was listed by the European Union as a “critical raw material” in 2020. The market size for the lithium battery is predicted to grow from $57bn (£45bn) in 2023, to $187bn (£150bn) by 2032.
To find promising alternatives to lithium batteries, it helps to consider what has made the lithium battery so popular in the first place. Some of the factors that make a good battery are lifespan, power, energy density, safety and affordability.
The downsides are also plentiful: at the end of their lifespan, recycling these batteries is still a complicated process. Extracting individual metals in the battery for recycling involves shedding the metal, then separating them in liquid to extract the desired metal.
“Recycling a lithium-ion battery consumes more energy and resources than producing a new battery, explaining why only a small amount of lithium-ion batteries are recycled,” says Aqsa Nazir, a postdoctoral research scholar at Florida International University’s battery research laboratory.
Lithium extraction using evaporation ponds, as is done in countries such as Chile, comes with a high water footprint. Studies show that contaminants may be released into the environment during the evaporation process, potentially affecting nearby communities. Water scarcity caused by mining could also threaten the livelihoods of indigenous communities. The overlap of mining sites with indigenous living areas has also led to forced migration and the abandonment of ancestral villages.
An alternative to the evaporation method is hard rock mining, such as is done in Australia. But this has its own drawbacks. For every tonne of lithium mined during hard rock mining, approximately 15 tonnes of CO2 is emitted into the atmosphere.
So, are there viable alternatives to the lithium-ion battery?
Sodium-ion batteries
In sodium-ion batteries, sodium directly replaces lithium. Not unlike lithium-ion batteries, sodium batteries contain four main components – the anode, the cathode, an electrolyte and a separator. The state of the electrolyte varies depending on the manufacturer.
The sodium to lithium ratio in the earth’s crust is 23,600 parts per million (ppm) to 20 ppm. The natural abundance of sodium leads to a much lower cost of extraction. Another factor for the sodium battery is that it can make use of other lower cost materials, replacing copper foils with aluminum foils, for instance.
Maria Forsyth, chair of electromaterials and corrosion sciences at Deakin University, Australia, says that switching from lithium to sodium battery production would be fairly low cost.
“Manufacturing wise, the transition is easy because the same factories, which currently produce lithium-ion batteries, can manufacture sodium batteries,” says Forsyth. “This means production can be scaled quickly.
One benefit of sodium batteries is their safety in transit. “A unique feature of sodium ion technology is the ability to discharge sodium to zero volts for storage and transportation,” says Quinn, Faradion’s chief executive. “This means it can be stored and transported in safer conditions.” The lower flammability risk levels make it a safer option compared to lithium batteries, Quinn says.
One drawback, however, is low energy density. For EV manufacturers, low energy density batteries are problematic because this affects a vehicle’s range. While lithium batteries have energy densities between 150-220 Wh/kg (watt-hour per kilogram), sodium batteries have an lower energy density range of 140-160 Wh/kg. Meng says this means it’s less likely that sodium batteries will be commercially scaled for use in EVs that require long ranges between charges.
Another hurdle is sodium batteries can only manage a short number of charging cycles in its lifespan. Currently, sodium batteries have a charging cycle of around 5,000 times, whereas lithium-iron phosphate batteries (a type of lithium-ion battery) can be charged between 8,000-10,000 times. But researchers are working to solve this – in 2023, scientists and engineers in China achieved 6,000 cycles using a different type of electrode.
China’s battery technology firm HiNa launched a 100 kWh energy storage power station in 2019, demonstrating the feasibility of sodium batteries for large-scale energy storage. HiNa has also recently piloted a batch of sodium battery powered electric vehicles.
Solid-state batteries
Solid-state batteries use solid electrolytes, instead of the liquid or aqueous electrolytes common in traditional batteries. The two most popular types of solid electrolytes include inorganic solid electrolytes (oxides and sulfides) and solid polymers (polymer salts, or gel polymers).
Using solid electrolytes reduces the risk of dendrite formation – those tree-like structures within the battery that can cause battery failure. Solid-state batteries also have a lower risk of flammability, a higher energy density and a faster charging cycle.
However, solid-state batteries may be harder to scale quickly than sodium batteries, says Shirley Meng, professor of molecular engineering at the Pritzker School of Molecular Engineering at the University of Chicago. “Sodium batteries are lower in cost, and are easier to integrate into current lithium battery production plants.” Based on a 2020 calculation model, the manufacturing costs of solid state batteries are also currently higher than that of lithium ion batteries.
To advance solid battery technology, it’s essential to find durable solid-state electrolytes. Some researchers say an ideal solid electrolyte is yet to be found. However, Colorado-based Solid Power has designed a sulfide electrolyte-based battery which it claims is 50-100% higher in energy density than modern lithium ion batteries. Solid Power aims to scale its solid-state tech to power 800,000 electric vehicles per year by 2028.
Solid-state batteries are currently commercially available in a thin-film format, making them an option for wearable electronics, “internet of things” (IoT) devices, for example home security systems and smart lighting. They can also be used in medical devices, such as llika’s Stereax M300, a hip implant device.
But while these batteries have some small-scale uses, they aren’t currently an option for large-scale energy storage. “We need to be realistic,” says Meng. “Right now, perhaps solid-state batteries are viable for IoT and wearables. But for solid-state tech that can contribute to the energy transition, they will need to be scaled to produce terawatt hours (TWh) of energy.”
Lithium-sulphur batteries
Lithium-sulphur batteries are similar in composition to lithium-ion batteries – and, as the name suggests, they still use some lithium. The lithium is present in the battery’s anode, and sulphur is used in the cathode. Lithium-ion batteries use rare earth minerals like nickel, manganese and cobalt (NMC) in their cathode.
Sulphur is more abundant in the Earth’s crust than nickel, manganese and cobalt and its extraction process is less resource intensive. It is also more widely available because it’s the by-product of natural gas processing and oil refining. Though supplies of sulphur may fall over the next few decades due to global decarbonisation The US alone produces 8.6 million tonnes of sulphur a year.
So although these batteries contain lithium, the abundance of sulphur makes them a potentially more sustainable option compared with conventional lithium-ion batteries, says Aqsa. “When commercialised, this battery will likely be used for grid storage, though mobile use is also feasible in the longer term.”
The similarity with lithium-ion batteries makes lithium-sulphur batteries relatively easy to produce. “They can be manufactured in the same production plants, saving costs of new technical resources,” says Nazir.
Lithium-sulphur batteries also have additional functional advantages as they have a higher energy density, meaning they produce more power, Nazir adds. “Sulphur has the capacity to move more electrons. Lithium-sulphur batteries have nine times the energy density of a lithium-ion battery.”
However these batteries suffer from poor chargeability. The formation of tree-like structures called dendrites can lead to short circuiting and battery failure. With prototypes working for as little as 50 charge cycles, they aren’t yet feasible for use in EVs, for example.
Lithium-sulphur batteries are already on the market, where they are used for gadgets requiring batteries with a lighter weight and a longer single charge time. In 2020, Korean chemicals company LG Chem successfully piloted a drone powered by a lithium-sulphur battery, and confirmed that the battery had a stable charge and discharge cycles. LG Chem intends to mass produce lithium-sulphur batteries with double the intensity of lithium-ion batteries by 2025. Meanwhile the German battery startup Theion is also working to bring lithium-sulphur batteries to electric vehicles.
If one thing is clear, it’s that no single battery type is going to be a universal answer to replacing lithium ion batteries. But as Forsyth points out, that’s not a bad thing.
“We don’t need to replace the lithium in all batteries, what is needed is a diversification of battery technology,” says Forsyth. “Maybe it’s not having one replacement but having alternatives that can be deployed where it’s right to deploy them.”