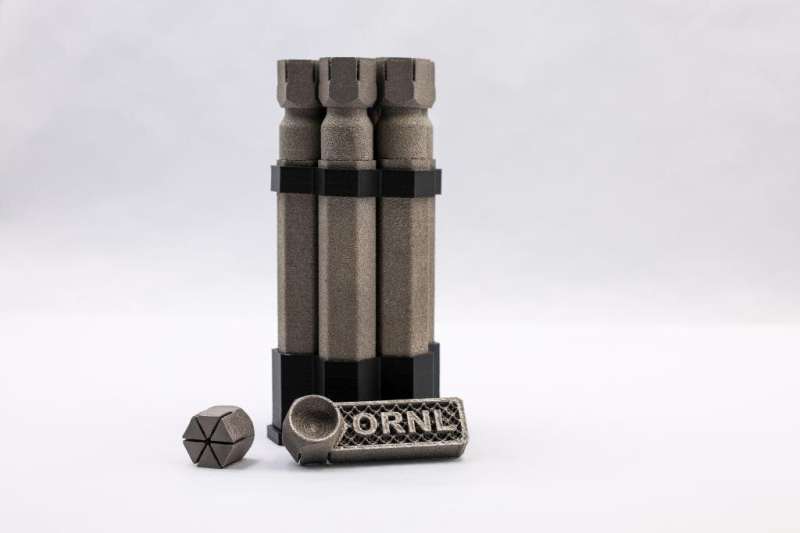
Researchers at Oak Ridge National Laboratory used additive manufacturing to produce the first defect-free complex tungsten parts for use in extreme environments. The accomplishment could have positive implications for clean-energy technologies such as fusion energy.
Tungsten has the highest melting point of any metal, making it ideal for fusion reactors where plasma temperatures exceed 180 million degrees Fahrenheit. In comparison, the sun’s center is about 27 million degrees Fahrenheit.
In its pure form, tungsten is brittle at room temperature and easily shatters. To counter this, ORNL researchers developed an electron-beam 3D-printer to deposit tungsten, layer by layer, into precise three-dimensional shapes. This technology uses a magnetically directed stream of particles in a high-vacuum enclosure to melt and bind metal powder into a solid-metal object. The vacuum environment reduces foreign material contamination and residual stress formation.
“Electron-beam additive manufacturing is promising for the processing of complex tungsten geometries,” said ORNL’s Michael Kirka. “This is an important step for expanding the use of temperature-resistant metals in energy resources that will support a sustainable, carbon-free future.”